Ideal for cutting and perforating
Your product is to be cut in a zigzag; e.g. Riffle Chips®? Do you squeegee longitudinal patterns in doughs; e.g. noodles? Do you need to perforate your product; e.g. tear-off films? Then the tooth blades and tooth knives from LUTZ BLADES are the right product for you.
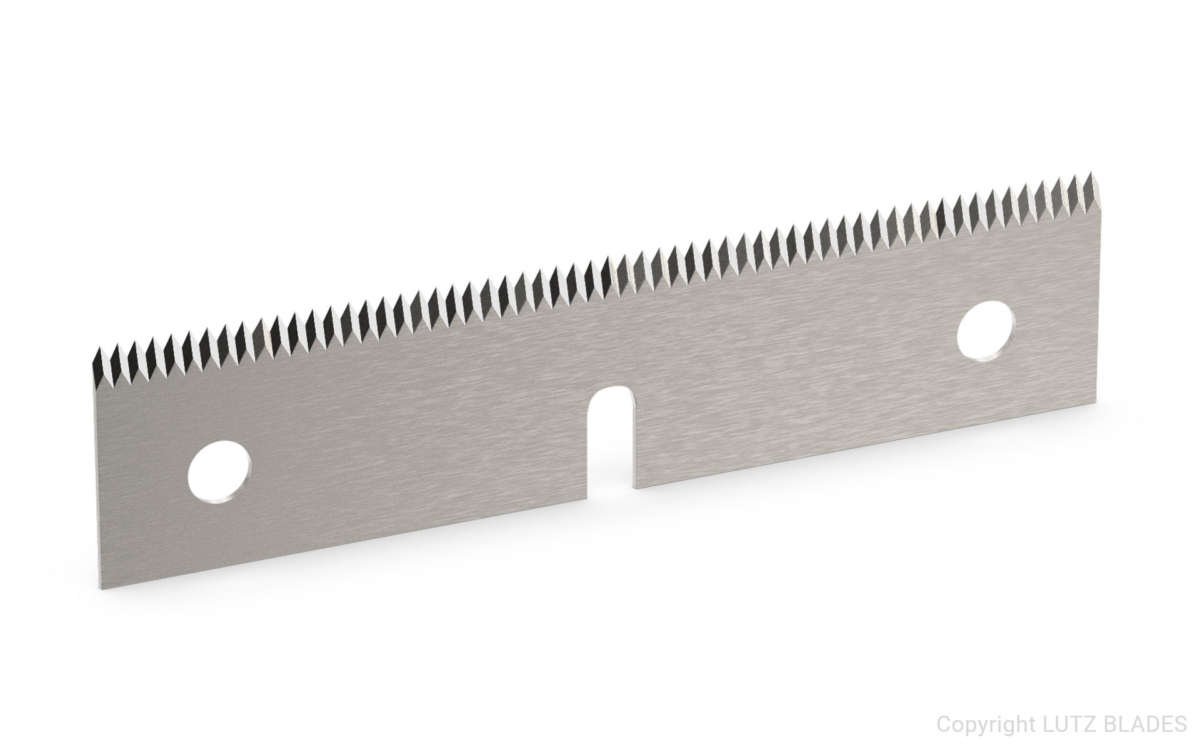
How you benefit
of LUTZ BLADES tooth blades and tooth knives:- Large selection of tooth pitches and angles
- High quality materials
- Individual advice
- Adjustment of the blade to your cutting application
How they are characterized
LUTZ BLADES tooth blades and tooth knives from:- Suitability for food
- Wide range of hard coatings to increase service life
- Pointed teeth to cut smooth or stretchy material
- Flat teeth for cutting soft materials
- Round teeth for long service life